Case Study: Large Global Pharmaceutical Company
Ricoh Partners with a Global Pharmaceutical Giant to Speed Up Regulatory Submissions and Eliminate Errors
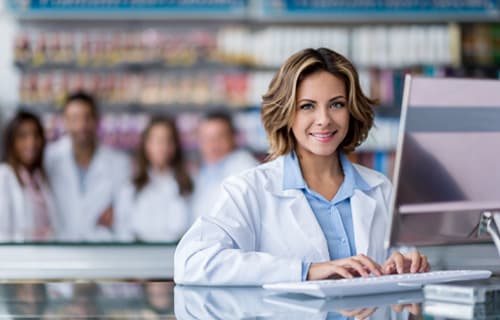
About the customer
A major global pharmaceutical company innovates and produces a variety of therapies for oncology, neuroscience, cardiovascular, metabolism and infectious diseases. With more than 40,000 employees around the world, the pharmaceutical giant has been in business for nearly 70 years, bringing life-enhancing drugs to market and healthcare relief to the world's population.
Since Ricoh assumed responsibility for the pharmaceutical company's production centers, the FDA and other regulatory bodies have not returned any submission packages for rework due to errors.
Challenge
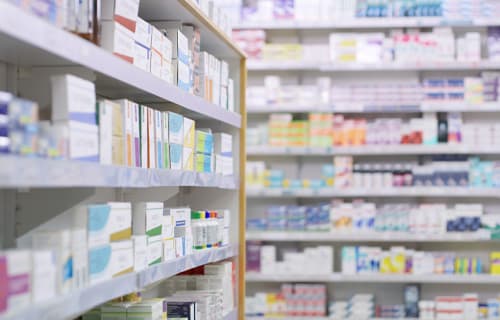
Complex regulatory approval process
Varied regional document requirements
Prolonged document submission times
Returned packages for missing documents or errors
Before any new drug can be released to the market, the pharmaceutical company had to gain regulatory approval — which involved a complex web of steps. Without this approval, all of the work that went into developing the new drug is potentially at risk.
While the U.S. Food and Drug Administration is the main regulatory body, every region of the world has their own regulatory entities with required protocols and preferences for reviewing documentation. Some want materials in paper booklet form, others want the materials on CDs or DVDs — and some want both. The materials consist of an initial briefing booklet and follow-up booklets explaining the drug, its intended uses and potential side effects. In addition, all promotional materials such as print, digital and television ads have to be approved by regulatory bodies to ensure claims are credible and not misleading.
The pharmaceutical company had in-house production offices around the world dedicated to printing, compiling and mailing all the regulatory documents and promotional materials to the regulatory bodies. However, these offices were operated by a downsized team due to cost pressures and recruitment challenges, which led to prolonged submission times and an increasing number of packages being returned due to errors or missing documents.
Solution
Ricoh's highly automated process for producing regulatory materials has sped up submission times by at least three to five days.
Managed Print Services for package production and assembly
Installed hardware and software to improve workflow
Rearranged workspace to increase efficiency and speed processing
Enlisted quality control measures
Ricoh assumed responsibility for production and assembly of document packages, establishing local submission offices in emerging markets staffed with personnel trained in regional requirements. The team conducted analysis on print volumes in the offices to determine the right staffing level for each location.
Leveraging workflow expertise, Ricoh also equipped each office with state-of-the-art hardware and software to manage the document production process and improve the overall workflow. Due to the nature of the highly regulated environment, all documents had to be stored in a secured content management system (CMS), which was inspected, reviewed and approved by the pharmaceutical company. Once up and running, the new workflow enabled our team to drop a file into the software, process it and select a printer destination. The software also tracked the number of tabs for each package and sent the printed documents to the appropriate tray. In addition, Ricoh went into problem-solving mode, organizing the equipment to streamline the workflow and make sure all of the materials were within arms reach — rather than scattered throughout the office — to improve production efficiency and turnaround times.
Rigorous quality control steps were followed throughout all of the processes. The team spot checked all printed documents to ensure they were in place, organized properly and smudge-free. If the document package required a CD or DVD submission, Ricoh reviewed the digital files to ensure all were on the disk. In addition, the team created and introduced a Service Excellence Operations Guide to ensure process continuity at all locations globally. Going forward, Ricoh is continuing to collaborate with the pharmaceutical company to bring more automation to the production process with solutions such as web submission software.
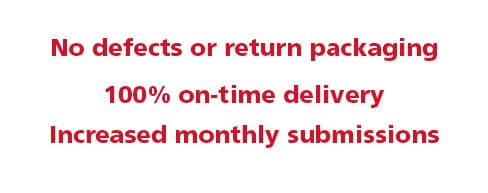
Results
No defects or returned packaging
100% on-time delivery of submissions
Reduced operational costs
Increased number of submissions per month
In the nearly seven years since Ricoh began producing the pharmaceutical company's regulatory documents, there have been no defects or returned packages. The Ricoh team has achieved 100% on-time delivery, helping the pharmaceutical company get their drugs approved and launched into the market as quickly as possible.
Also, the pharmaceutical company's operating costs have been reduced with Ricoh's on-site staffing model. In addition, the team has improved productivity and increased the number of monthly regulatory submissions globally — typically 100 or more per month. Furthermore, the highly automated production process has sped up submission times by at least three to five days.
The pharmaceutical company was so pleased with Ricoh's technology and expertise that additional scanning work has come into the production office from other departments unrelated to regulatory submissions.